I laid out the bottom panels and glued them together. I meant to do this earlier today, but I got flummoxed and thought, rather than make a big mistake, just do nothing. Wait until you’re settled about what you mean to do.
A few hours later, I decided to do this: (1) stretch the string baseline really tight (it damn near twangs) then (2) lay out the middle section parallel to the string and about 1/8 inch off it. Because I’m working from a kit comprised of CNC-routed panels, I don’t really have to worry about all the offsets shown in the plans. If I lay out the first and last points of the end pieces, all the specified offsets in between will fall where they should. I began by putting the middle section exactly where I wanted it with respect to the taut string and (3) taped down its chine-edge.
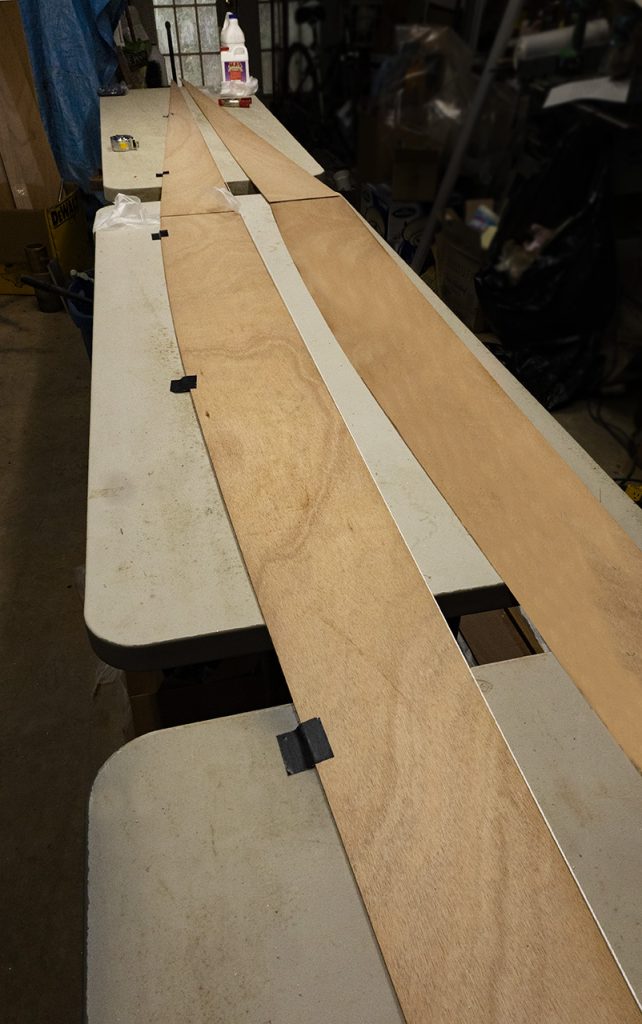
Next, epoxy,and then stack the bottom panels shown on the right atop those on the left.
…
Then (4) I put the bow and stern sections where they belonged by aligning the scarfs and the offset at the tips of the bow and stern with respect to the string by the distance specified (one inch). After making sure that the keel line was straight and that the chine traced a fair line (sanity checks), I (5) put plastic between the scarfs and the table. (6) I drizzled epoxy over the scarfs. The second set of bottom panels is identical to the first; when assembled, each will be a reflection of the other, symmetric around the keel line. So (7) I put plastic down over the first joints and (8) laid the second set of panels exactly atop the first. (9) I added epoxy to their joints; (10) covered the scarfs with plastic film, and (11) put some weight on top.
Stacking the pieces this way insures that if the bottom panels are not perfect, they are at least identical in their imperfection. That will make life easier than if they were in any way different. For the record, the drawing says the bottom panels should be 19 ft 6 and 3/4 inches from end to end. Mine measure 19 ft 6 and 7/8 inches. I think the difference of 0.05% is reasonably close to plan. (Most of that precision is due to CLC’s CNC routers; kudos.)
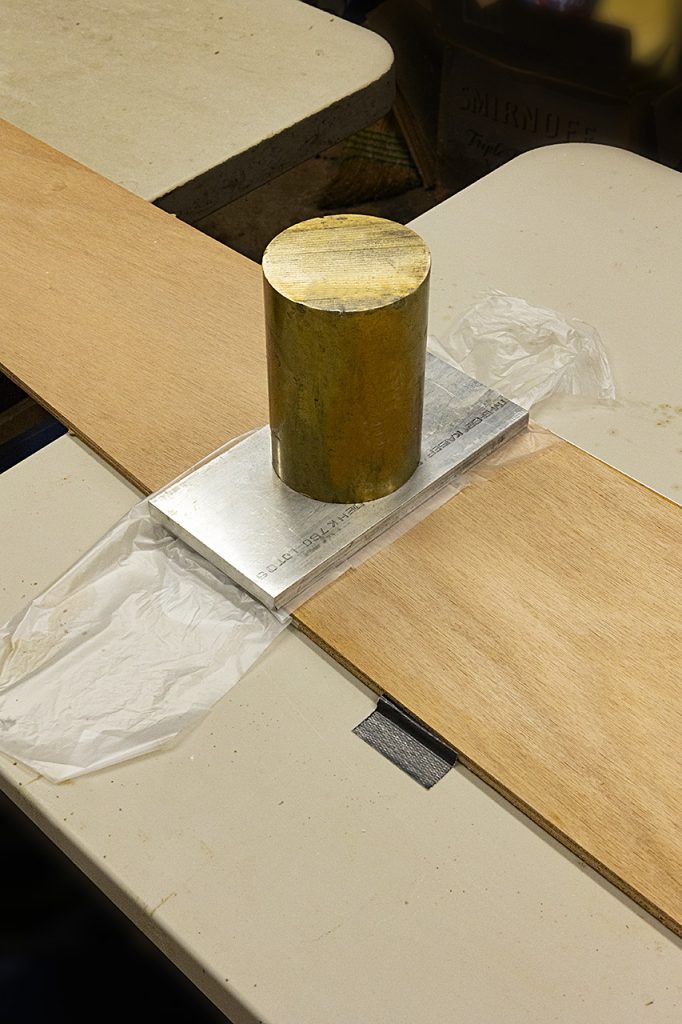
telescope projects come in handy.
…
It’s 62°F in the shop this evening. Today’s epoxy mix is 18g + 9g + a couple of pinches of wood flour. I walked away from the work bench at 6:30 PM. Later this week, nightly lows may seep into the basement and make it marginally too cool for putting down epoxy. I draw the line at 60°F, but I am advised that that’s both conservative and arbitrary and that epoxy will cure at lower temperatures. “Eventually.” Next I get to try stitching.
Tomorrow
I’ll start by drilling holes in the hull, about 200 of them, which seems an odd thing to do on the way to making a boat.